Here we can provide you with all calibration solutions such as (Temperature, Pressure, Weight …..etc) . Aslo we have the Torque measurement system to prevent your ship from breakdown cost. The flowmeters and vibrations sensors are very important to provide you with accurate measuring .
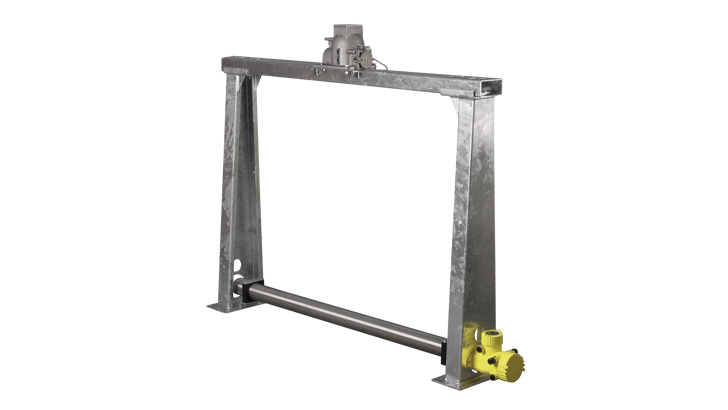
Radiometric
VEGA WEIGHTRAC 31
WEIGHTRAC 31 is used for weighing all types of materials on belts, chain conveyors, screw feeders, vibration conveyors and other conveying systems.
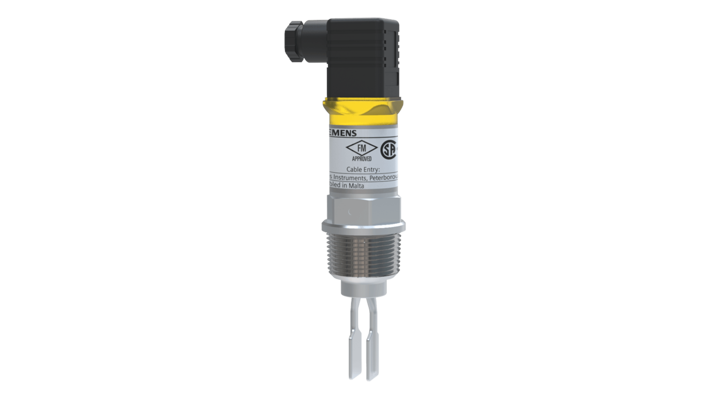
Level switch - Liquids
Siemens SITRANS LVL100 Point Level Switch
Universal level switch for liquids. Used at process temperatures between -40...+150 °C and at a process pressure of up to 64 bar.
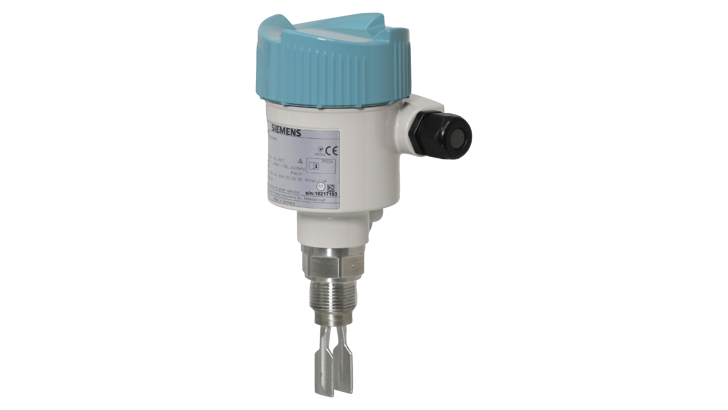
Level switch - Liquids
Siemens SITRANS LVL200 Level Switch
The SITRANS LVL200 is a reliable level switch with a vibrating fork. Typical applications include level measurement, overfill protection, and dry-run protection. Its compact design allows it to be used in small pipes and applications with limited space. Additionally, it can be used under challenging conditions, including turbulence, air bubbles, foam formation, buildup, or external vibration.

Level switch - Liquids
VEGASWING 51
Level switch for liquids - standard version - 40mm forks. Typical applications will be overflow, overflow and dry run protection.
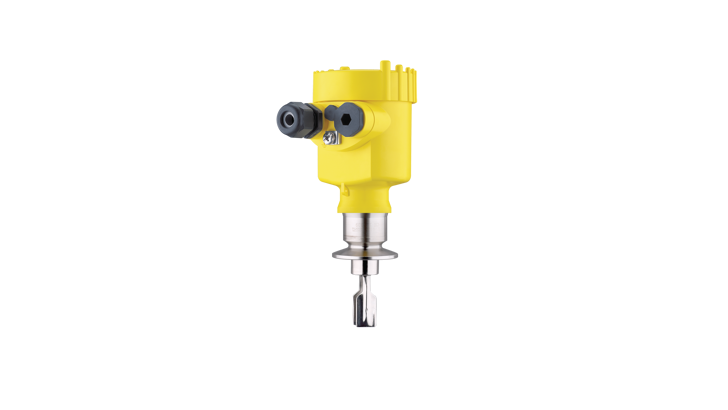
Level switch - Liquids
VEGASWING 61
Versatile level switch - used for almost all liquid applications. Typical applications will be overfill or dry run protection.
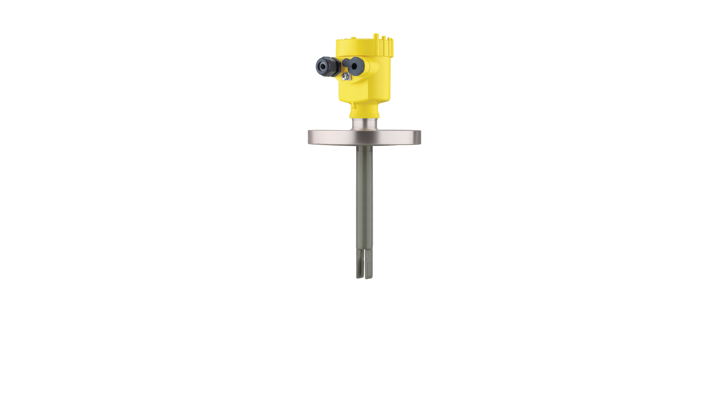
Level switch - Liquids
VEGASWING 63
Versatile level switch - variable insertion length - is used for almost all liquid applications. It's also a reliable instrument in high viscous media.
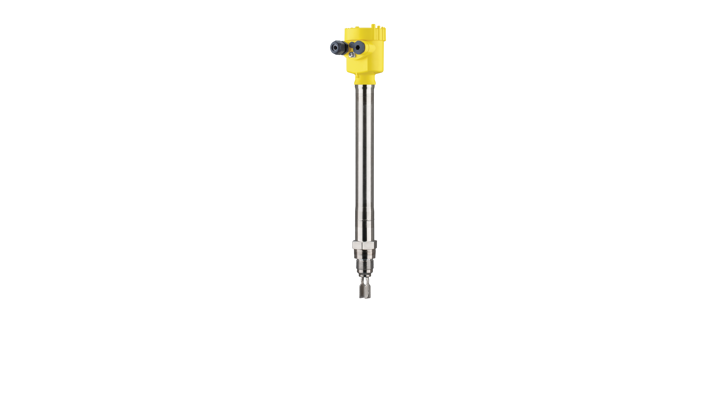
Level switch - Liquids
VEGASWING 66
Level switch to extreme temperature. compact instrument or with pipe extension up to 6m. Various supply options in Ex areas.
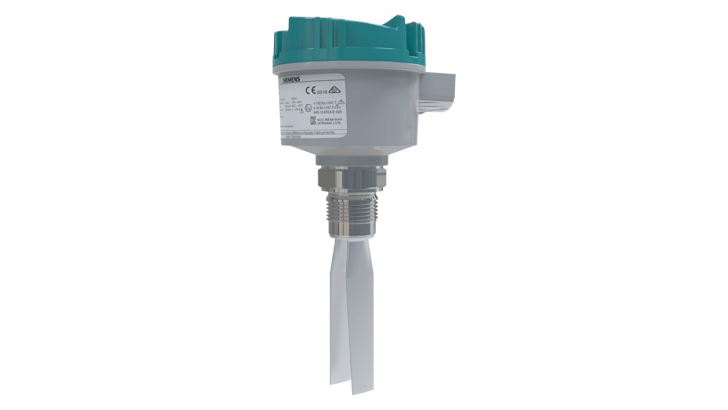
Level switch - Bulk solids
Siemens SITRANS LVS100 Level Switch
Level switch for solids at process temperatures between -40...150°C and pressures up to 10 bar. Ideal for use in silos, containers, and hoppers in the cement, food, power, plastics, and general industries.
No results found
Marine Instruments
The importance of using proper instrumentation Electrical and mechanical instrumentation invovles design, control and implementation of devices that can measure physical quantities. There is a huge amount of thought behind the proper instrument and installation choices for each small or larger measuring point. All vessels generally use state of the art instrumentation and equipment to manage everything from the engines, steering and navigation system. When the equipment malfunctions it can have a huge impact on the operational efficiency and can cause massive downtime that can put the vessel behind schedule. A broken viscoity sensor can cause wrong engine combustion, wrong additive dosing can reduce fuel efficency or worse; lubrication properties of various lubration oils. A ballast that isnt filled appropriately after loading can impact vessel stability and leaks and dangerous pressure levels in fuel tanks can impact enginre operation or even lead to disaster.
Proper Use of the Correct Instrumentation Is Important
– a Sensor Is Not Just a Sensor
Today’s fleet is generally becoming highly sophisticated operations with equally sophisticated equipment on board. And controlling all this sophisticated equipment correctly and preventing breakdowns is crucial to a smooth and cost-effective operation. Choosing the correct instrument for measuring the processes on board is not only a good idea seen from a practical aspect, but investing the time and possibly a little extra money on instrumentation that is ideal for the task, can ultimately save the vessel both cost and unnecessary interference for the crew on board.
Measurements are used all over the modern ship in order to keep equipment running at optimum conditions. Everything from critical installations such as main engines, auxiliary engines, steering and navigation to other installations such as cranes, cargo pumps and wastewater handling can and should be monitored with optimization in mind. Optimization of processes on board a ship can contribute to better earnings and lower emissions – even if the realized optimization is only constituted by fewer unplanned interruptions such as maintenance works and breakdowns.
A malfunctioning viscosity sensor can cause lower exploitation of the fuel due to wrongful combustion; a hydraulic failure on a crane can cause delay in port operations and interrupt the planned schedule; incorrect ballast control can impact vessel stability and trim causing anything from slightly lower performance to accidents and undetected leaks in cargo and fuel tanks can cause dangerous situations or even lead to disaster.
Choosing the correct instrument for a specific task can be challenging, as a myriad of variations of a single instrument often exist. And just going by the most expensive option or for something that has been recommended, is not always the right way, as the process and media in which the instrument should be installed is what determines what measurement principle and setup should be chosen. Degradation is caused very differently based on what the instrument is exposed to, and one instrument suited for one place on board might be unsuitable for another; a different pressure might cause inaccurate reading or mechanical failure and a different media could do the same.
Across the specialists at Insatech, we have the knowledge and experience to find the right instrument for your specific application as well as we can guide you to install it correctly. Making your operation as smooth and efficient as possible is always our goal with our counselling and services, as your success leads to our success!